Facade Panels with HPL
The invention of High-Pressure Laminate (HPL) panel manufacturing technology dates back over a century. Its initial use as cladding for external building walls began in the 1960s. Despite its long history, HPL facade panels remain relevant today as a modern cladding material for various structures, including buildings. These panels find extensive application in the realm of Ventilated Facades (VF).
Let’s delve into the details of the production of facade HPL panels and what this material entails. HPL, an acronym for High-Pressure Laminate, is created by bonding specially treated cellulose layers under high pressure and temperature. The result is a monolithic, robust material. Based on purpose, decorative panels for interior and exterior applications are distinguished. Let’s focus more on the latter to understand the characteristics that differentiate them:
- Coating presence: single-sided or double-sided.
- Thickness options: 6-8-10-12 mm.
- Sheet sizes: 3050×1220, 2800×1300, 3050×1300, 4200×1860, 2440×1220 mm.
Examining panels for external use, designed to withstand various climatic conditions throughout the year, it’s important to highlight UV resistance and colorfastness. The panels also boast fire resistance, absence of toxic substances, and a protective film made of specialized resin.
They are widely used for cladding ventilated facades, balconies, partitions, balustrades, and more. Additionally, the panel edge (core) deserves mention, requiring no additional processing immediately after cutting. Typically, the core comes in dark, black, or brown colors. Moreover, this material has significant density, twice that of MDF.
HPL panels offer numerous advantages, with key points including:
- High strength: Resistant to mechanical damage.
- Diverse designs: Available in a wide range of colors, textures, and decorative options, including imitation of natural materials like wood, metal, textile, stone, etc.
- High wear resistance: Excellently withstands intensive use and wear, resistant to scratches, friction, moisture, and high temperatures.
- Easy installation: External walls made of panels are formed quickly due to their simple installation system.
- Fire resistance: Panels exhibit high resistance to fire, are difficult to ignite, and have a low burning rate.
- Longevity: HPL panels have a long service life and high UV radiation resistance, maintaining brightness and quality over an extended period.
By using HPL facade panels, cassette structures are obtained. The manufacturing of facade cassettes occurs on precision CNC equipment using special milling operations, including contour cutting, bevel removal, material extraction to the required depth, and assembly using mounting hardware (tube, angle, rivet, special adhesive).
When ordering HPL facade cassettes from Cut Facade, you benefit from an individual approach, qualified staff using modern CNC equipment, ensuring precision. Opting for a turnkey cassette supply means enjoying several advantages, including time savings, competitive material prices, affordable processing costs, and a professional approach. Upon agreement, our company also provides delivery of finished products to the customer’s site.
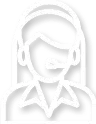
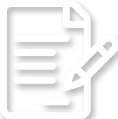

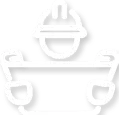
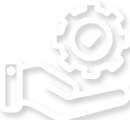
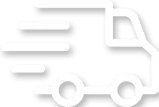