Facade Cassettes from Aluminum Composite Panels (ACP)
In the past few decades, the field of construction, particularly the installation of ventilated facade systems, would be hard to imagine without the term “aluminum composite panel” (ACP). This widely used material is also referred to as aluminum composite or simply composite, where the name itself implies its compositional nature, being a multi-component structure with aluminum as a key component. Essentially, this panel consists of two pre-painted aluminum sheets bonded together with a filler in between. ACPs are distinguished by thickness, ranging from 2 to 6 mm, with the most common panels being 3 and 4 mm thick. Based on the overall thickness, panels have corresponding layers of aluminum, such as 0.20-0.21-0.23-0.25-0.30 mm for three-millimeter panels and 0.25-0.35-0.40-0.50 mm for four-millimeter panels. Among these characteristics, the standard thickness for 3 mm panels is 0.21 mm of aluminum, and for 4 mm panels, it is 0.4-0.5 mm.
Let’s delve into the details of the ACP sandwich:
- Protective film;
- Coating:
– PE (polyester) – a coating based on polyether (bright glossy tones);
– PVDF (polyvinylidene fluoride) with a content of fluorocarbon powder (significantly higher color resistance);
– Nano coating (self-cleaning property and higher gloss compared to polyester or PVDF);
- Aluminum sheet;
- Filler:
Polymer filler:– HDPE (high-density polyethylene, known as low-pressure polyethylene) /
– LDPE (low-density polyethylene, known as high-pressure polyethylene);
Mineral filler:
– 70% aluminum trihydrate and polyethylene;
– 90% aluminum trihydrate and polyethylene;
- Aluminum sheet;
- Protective coating.
It is not surprising that this material has found special application in creating exteriors of buildings and structures. Composite panels are used for cladding facades, entrances, cornices, friezes, eaves, slopes, balconies, perforated facades, decorative screens for air conditioning units, and more. Simultaneously, the synergy of aluminum-composite cassettes with translucent structures (TSS) should be emphasized. Due to the harmonious combination of glass with the composite, the external wall becomes an ornament of the building. Additionally, composite cassettes on the facade can successfully blend with other facade materials, including HPL panels. The lightweight nature allows cladding even tall structures. For example, the weight difference of a 4mm ACP compared to a solid aluminum sheet is one and a half times, and compared to a steel sheet, it is four times. Weight data for panels from various manufacturers in the Ukrainian market are provided in the table below:
Panel Thickness (mm) | Aluminum Layer Thickness (mm) | Weight (kg/sq.m). |
3 | 0,21 | 3,5 – 3,75 – 3,8 – 3,9 – 4,29 |
4 | 0,23 – 0,30 – 0,40 – 0,50 | 4,5 – 4,8 – 5,1 – 5,6 |
It’s also important to consider the sheet size, which directly affects composite facade cassettes and their cost when detailing. Different manufacturers offer different sheet sizes, including widths of 1000-1500 mm and lengths of 2440-6100 mm. Standard width parameters are 1250-1500, and lengths are 5600-5800 mm.
Although cladding with ACP is sometimes referred to as aluminum facade cassettes, there are significant differences when comparing cassettes made from aluminum sheet and ACP of similar thickness. Firstly, the cost is significantly lower, and secondly, technologically, aluminum is not easily painted, whereas ACP has a factory-special coating with numerous shades, ensuring long-term use and integrity. When it comes to the production of metal facade cassettes, besides the weight difference, the ability to choose various textures, patterns, and the anti-corrosion properties of the composite are crucial factors.
Types of ACP Cassettes
Based on the shape, ACP cassettes are classified as simple or complex (cornice, corner), which also influences their price.
Manufacturing is carried out using CNC milling and engraving machines. V-shaped grooving is done for 3-4 mm sheets, with milling at angles of 45, 90, and 145 degrees, ensuring precise cutting and maintaining the straight angles of cassettes.
Purchasing cassettes follows this workflow:
- Receipt of customer input data (drawings, sketches, photos, dimensions).
- Development of drawings, if necessary, 3D modeling.
- Approval of drawings by the customer.
- Advance payment.
- Preparation of production files.
- Manufacturing (cutting, milling, forming).
- Optional assembly for cassette with assembly – cutting, milling, forming, assembly.
ACP sheets are either supplied by the customer or delivered by the company, depending on individual agreements. For assembly operations, fastening and assembly materials are provided by the customer (pipes, angles, rivets).
By special arrangement, assembled products are delivered to the site upon request of the installers. Cut Facade’s composite cassettes offer professionalism, quality, and convenience.
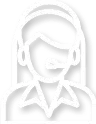
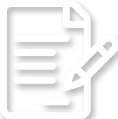

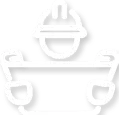
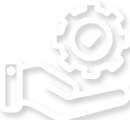
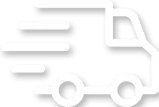