Facade panels
In contemporary construction, the application of ventilated facade systems (VFS) stands out as one of the most technologically advanced methods for exterior wall finishing. Beyond enhancing the aesthetic appeal and enabling the realization of ambitious architectural ideas, this approach is also driven by improved thermal insulation characteristics of the facade. The key feature of VFS involves constructing an additional wall positioned in front of the existing one, creating a specific air gap between them. This ventilation gap facilitates constant airflow from bottom to top, ensuring continuous circulation of air and removal of excess moisture from the walls or insulation, which may occur due to temperature variations inside and outside the building during colder seasons.
A typical ventilated facade comprises the following components:
- Framing subsystem with brackets and specialized profiles (mostly made of aluminum).
- Insulation layer (mineral wool, polystyrene).
- Windproof membrane.
- Cladding siding made of panels of various sizes (facade cassettes).
Furthermore, a notable advantage of such facade systems is the use of advanced lightweight materials, particularly specialized cladding facade panels. Among the most common and versatile are aluminum composite panels (ACP), consisting of layers of aluminum, pressed filler, and another layer of aluminum, with a finishing PE, PVDF, or Nano lacquer coating. To meet diverse exterior requirements, manufacturers offer a variety of coatings to choose from:
- Matte.
- Glossy.
- Metallic.
- Mirrored.
- Pearl.
- Textured.
- Patterned.
Increasingly, High-Pressure Laminate (HPL) panels gain popularity as facade cladding. Produced by bonding layers of cellulose under pressure, the external appearance and texture make this material quite popular.
Examining these aforementioned facade panels and cassettes in more detail, considering their constituent materials and processing methods, it is crucial to emphasize a significant advantage shared by both types – their anti-corrosion properties. Additionally, it’s worth noting that ACP cassettes can be used to clad facades of varying heights.
The calculation of facade cassettes begins with the optimal layout of unfolded details of specific dimensions on the material sheet, known as a “cutting plan.” The next step in cassette production involves cutting and milling for ACP and cutting and chamfering for HPL. Subsequently, assembly and shaping take place (optional).
Facade cassettes from the manufacturer Cut Facade are produced using modern Computer Numerical Control (CNC) machines. The ACP and HPL cassette production process is automated and entirely controlled by operators. Skilled professionals carry out the manufacturing of these cladding elements in proper conditions within a dry workshop. A tailored approach, consideration of customer preferences, fair pricing, and adequate processing costs are all prerequisites for successful collaboration.
To purchase facade cassettes, having the relevant drawings and knowing the type and thickness of the material, is quite straightforward. To do so, simply submit a request for a quote, providing the basic input data or contact our sales department by phone.
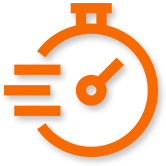
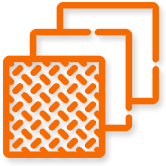
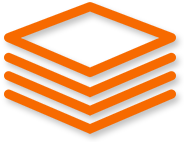
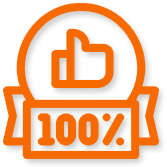
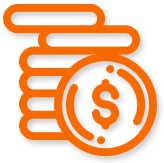
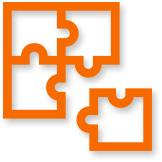